In the world of modern construction, the demand for lightweight, durable, and aesthetically pleasing building materials is on the rise. Among these innovative solutions is the Composite Panel, also known as Aluminum Composite Panel (ACP). Comprised of a sandwich-like structure of two thin aluminum sheets with a core material in between, ACP offers exceptional strength, flexibility, and design versatility.
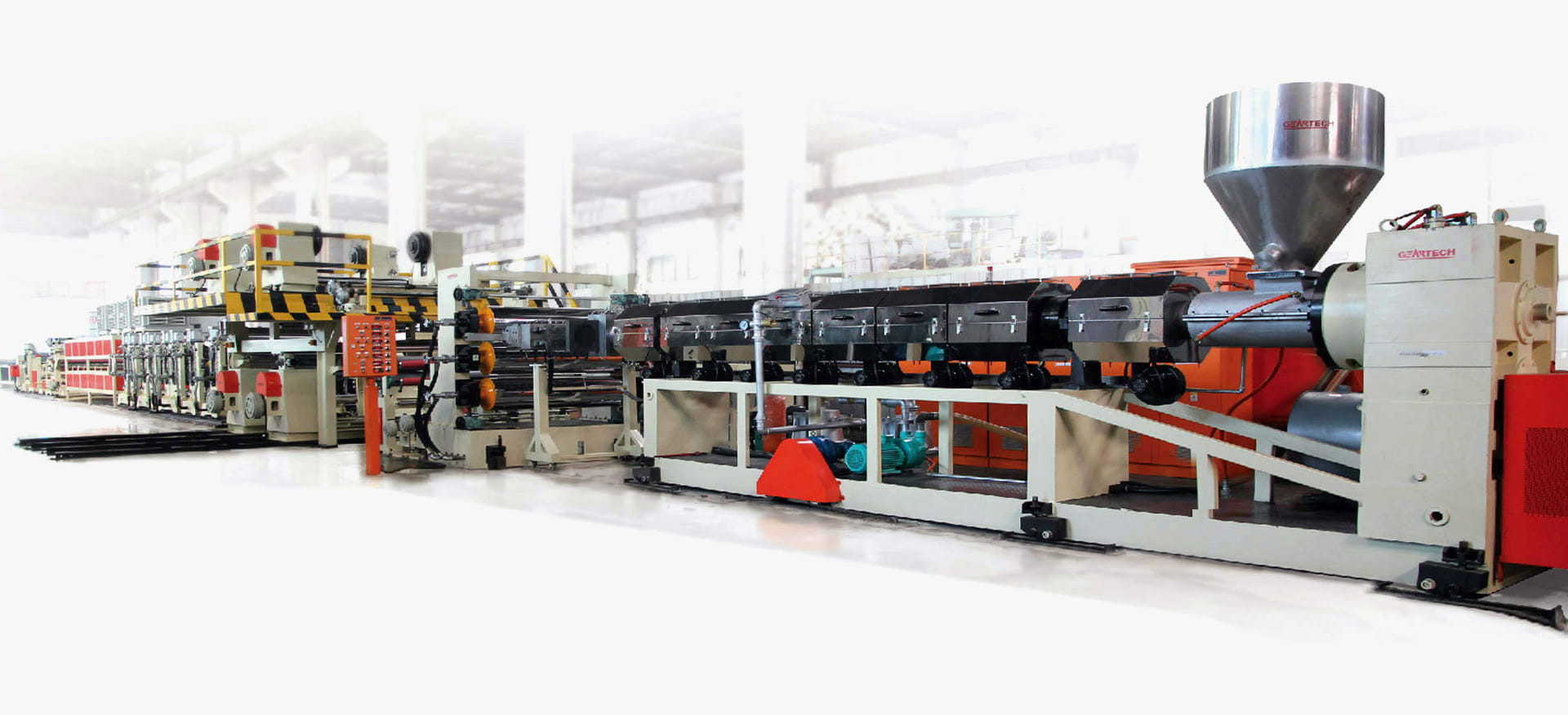
The Manufacturing Process of ACP:
The production of ACP involves several key steps, each contributing to the creation of a high-quality composite panel. Let's take a closer look at these stages:
a. Core Material Preparation:
The core material of an ACP can be made of various substances such as polyethylene (PE), mineral-filled polymer, or fire-resistant material. The core material is prepared and processed to meet the desired specifications, including thickness and density.
b. Coating:
The two thin aluminum sheets that form the outer layers of the composite panel are coated to enhance their durability and resistance to corrosion. The coating process typically involves applying a protective primer, followed by a color coating or a protective film.
c. Adhesive Application:
A specialized adhesive is applied to both sides of the core material. This adhesive layer facilitates the bonding of the core material with the aluminum sheets, ensuring structural integrity and stability.
d. Composite Panel Assembly:
In this crucial stage, the coated aluminum sheets are carefully aligned with the adhesive-coated core material, forming a sandwich-like structure. The assembly is then subjected to high pressure and temperature using a specialized laminating machine, enabling the adhesive to bond securely with the aluminum sheets and the core material.
e. Trimming and Finishing:
The composite panel is trimmed to the desired dimensions using precision cutting tools. Additionally, various finishing treatments such as edge sealing, grooving, and perforations can be applied to meet specific design requirements.
The production of ACP relies on advanced machinery and equipment that streamline the manufacturing process. Here are some of the key components typically found in ACP production lines:
a. Uncoiler and Coil Feeding System:
Uncoilers are used to unwind aluminum coils, which serve as the source material for the ACP production. The coil feeding system ensures a continuous and smooth supply of aluminum sheets throughout the production line.
b. Coating Line:
The coating line consists of coating machines equipped with rollers or spray systems to apply protective coatings, such as primer and color coatings, on the aluminum sheets.
c. Laminating Machine:
The laminating machine is a critical component where the assembly of the composite panel takes place. It applies heat and pressure to bond the aluminum sheets with the adhesive-coated core material.
d. Trimming and Cutting Equipment:
Precision cutting tools, such as CNC routers or saws, are employed to trim the composite panel to the desired dimensions and achieve clean and accurate edges.
e. Finishing Systems:
Various finishing systems, such as edge sealing machines, grooving machines, and perforation equipment, add the final touches to the composite panel, enhancing its appearance and functionality.