In today’s metal finishing industry, manufacturers are placing greater emphasis on consistency, especially when it comes to the production and application of color coated aluminum coil. While the technology behind steel coil coating has evolved over the years, the current focus is on achieving uniform results across large volumes, ensuring that every coil meets performance expectations.
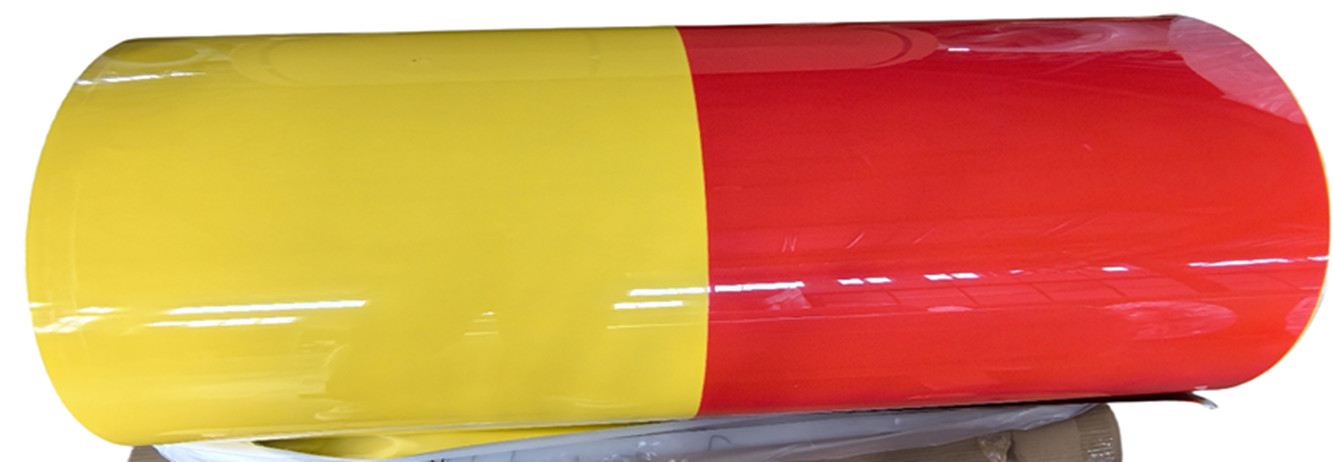
One of the main reasons for this renewed attention to consistency is the rising demand from sectors like construction, automotive, and interior design. These industries require not just visually appealing finishes but also coatings that behave predictably during fabrication and over time. A color coated aluminum coil must have the same surface properties, thickness, and adhesion levels from one batch to the next. Inconsistent coatings can pilot to problems such as peeling, uneven coloration, or reduced corrosion resistance.
While equipment upgrades and automation have helped improve results, human oversight still plays a vital role in monitoring the steel coil coating process. Operators are now more engaged in checking for variations in temperature, line speed, and paint viscosity. Small changes in these factors can affect how well the coating bonds to the surface. To less errors, more facilities are adopting real-time quality tracking and predictive maintenance systems, aiming for fewer production interruptions and better overall control.
In addition to the mechanics of the process, material quality is another key consideration. Both color coated aluminum coil and steel substrates need to be clean and defect-free before entering the coating line. Surface preparation methods such as degreasing and chemical treatment help improve the coating’s ability to adhere uniformly. Many producers are investing in more precise surface prep equipment to support this goal. The choice of paint or coating solution also matters; compatibility between the substrate and coating can greatly impact consistency, especially under varying environmental conditions.
Interestingly, the emphasis on uniform application doesn’t mean sacrificing flexibility. Manufacturers still need to meet custom requirements in color, gloss, or texture. The challenge lies in delivering those variations without compromising on quality. For instance, one project may call for a matte color coated aluminum coil with high scratch resistance, while another might need a glossy finish for decorative panels. In both cases, the coating must remain even and stable throughout the roll.
As for steel coil coating, the shift toward eco-friendly solutions has added another layer of complexity. Water-based and low-VOC coatings are now common, but they behave differently compared to traditional solvent-based products. These newer coatings demand tighter control over environmental conditions during application, such as humidity and airflow. Manufacturers are learning to adapt their processes accordingly to maintain consistent outcomes.
Training has also become a bigger part of the conversation. Teams involved in steel coil coating are being trained not just in machine operation but also in understanding how different materials and settings influence the final product. This broader knowledge base helps reduce trial-and-error during production, improving consistency and reducing waste.
The market continues to grow, and with it comes pressure to meet higher volumes without sacrificing reliability. Whether it’s a color coated aluminum coil used for roofing systems or a steel coil coating applied to appliance panels, buyers expect materials that perform as promised. That expectation is pushing manufacturers to fine-tune their methods and focus on stability across the board.