China PE Color Coated Aluminum Honeycomb Composite Panel Coil
The demand for PE color-coated aluminum coils has been steadily increasing across various industries, owing to their versatility, durability, and aesthetic appeal. As the need for high-quality, long-lasting materials rises, the manufacturing processes of PE color-coated aluminum coils have evolved to meet the specific demands of modern applications. PE color-coated aluminum coils are widely used in construction, automotive, and decorative industries, with continuous innovations in their production ensuring that these materials continue to serve a broad range of needs effectively.
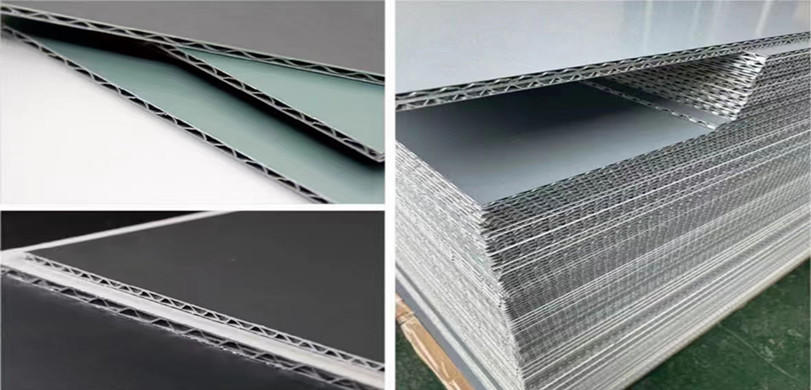
PE color-coated aluminum coils are produced by applying a layer of polyethylene (PE) coating onto an aluminum substrate. This coating provides a protective layer that improves the coil’s resistance to environmental factors such as corrosion, UV radiation, and bad weather conditions. The process of manufacturing PE color-coated aluminum coils involves several critical stages that contribute to the final product's performance and appearance.
The one step in the production of PE color-coated aluminum coils involves preparing the aluminum substrate. Aluminum sheets are carefully cleaned and pre-treated to remove any dirt, oils, or oxides from the surface. This step is essential to ensure the proper adhesion of the PE coating. The aluminum is then fed into a coil coating line where the coating process begins. In this phase, the aluminum coils are coated with a PE layer, which is typically made up of high-quality resin and pigment.
One of the key innovations in the manufacturing process of PE color-coated aluminum coils is the development of advanced coating techniques. The use of roller coating technology has significantly improved the efficiency of applying a uniform coating layer. Roller coating allows for precise control over the thickness of the PE coating, which directly impacts the coil's durability and resistance to weathering. Additionally, the incorporation of curing ovens in the process ensures that the PE coating is fully bonded to the aluminum surface, enhancing the coil's overall performance.
Another innovation in the production of PE color-coated aluminum coils is the development of specialized coatings designed for specific applications. For example, some coatings are formulated to provide additional protection against pollutants and industrial chemicals, making them suitable for use in harsh industrial environments. Other coatings are designed to enhance the aesthetic appeal of the coils, offering a wide range of color options and finishes to meet the demands of the construction and design industries. These specialized coatings are developed through extensive research and testing to ensure they meet the unique requirements of each application.
The continuous improvement of the PE color-coated aluminum coil manufacturing process has also led to the development of more sustainable production techniques. For instance, advancements in the recycling of aluminum materials have made it possible to reduce waste and less the environmental impact of production. Additionally, innovations in coating formulations have led to the creation of eco-friendly PE coatings that are free from harmful solvents, further promoting sustainability in the manufacturing process.
The versatility of PE color-coated aluminum coils makes them suitable for a wide variety of industrial applications. In the construction industry, PE color-coated aluminum coils are commonly used for roofing, wall cladding, and window frames. The durability and resistance to corrosion provided by the PE coating make these coils an ideal choice for buildings exposed to harsh weather conditions. In the automotive industry, PE color-coated aluminum coils are used for vehicle parts such as trims, body panels, and bumpers, where both strength and aesthetic appeal are crucial.
In addition to construction and automotive uses, PE color-coated aluminum coils are increasingly being employed in the production of household appliances, signage, and even electronics. The ability to customize the color and finish of the coating ensures that the coils can meet the specific needs of diverse applications. Furthermore, the lightweight nature of aluminum makes PE color-coated aluminum coils an attractive option for industries seeking to reduce the weight of their products without compromising on strength or durability.
In conclusion, the manufacturing processes of PE color-coated aluminum coils have seen significant innovations over the years, with advancements in coating technology, environmental sustainability, and application-specific designs. These innovations have allowed PE color-coated aluminum coils to become an essential material in a wide range of industries. As the demand for high-performance, durable materials continues to grow, the future of PE color-coated aluminum coils looks promising, with further improvements in production methods expected to meet the evolving needs of various industrial sectors.