As a new type of building decoration material, aluminum composite panel has experienced many years of ups and downs since its birth in the 1960s.
Some of them have metallic luster, transforming with colorful shapes, and gracefully adorn various spaces. As the world's recognized largest construction site, China has also become the world's largest aluminum-plastic panel consumer market, which has greatly promoted the advancement of the aluminum-plastic panel industry.
The development of aluminum composite panels, like other imported products, has also experienced a series of processes such as export, joint venture, and domestic production. Some old-fashioned aluminum-plastic composite panel equipment manufacturers have been paying close attention to the development of aluminum-plastic composite panels since the early 1990s. These manufacturers use their years of experience in plastic machinery and other industries, combined with the characteristics of aluminum-plastic composite panels. In the mid-1990s, it successfully developed the first fully automatic continuous hot rolling production line in China. At first, the product was positioned in the fully automatic continuous hot rolling production process. Judging from today's development, the product positioning was accurate at that time. Only the thermal compounding process can ensure the smoothness, adhesion, continuity and efficiency of production, and truly realize large-scale industrial production. In the early stage of equipment research and development, there is no reference material, it is based on product analysis, processing experience, and a relatively in-depth understanding of temperature, pressure, tension and speed control methods, especially for the most critical roller penetration of composite equipment. after research. In the whole production line, the heating method used requires that the rollers of different sizes have a smooth surface, high hardness, and the temperature difference at each point of each roller is controlled within ±1 °C. High-precision equipment and practical technology make the control of the entire production line extremely simple and effective. After several generations of product modifications, now each compound production line only needs 6 operators to complete the material from PE to aluminum-plastic All aluminum-plastic composite panel complete sets of equipment for the stacking of finished panels include aluminum coil surface pre-treatment production line, aluminum coil coating production line and aluminum-plastic composite panel composite production line.
At the beginning of equipment manufacturing, researchers spent a lot of energy to study the characteristics of the aluminum composite panel material itself, fully understand the advantages of its application in the construction industry, and constantly refer to the production of similar products.
The principle, with the deepening of understanding, also has a deeper understanding of its production process, a more unique point of view. In the seemingly complicated process of going to school, we believe that the most critical point is the combination of compounding temperature and pressure. The compounding temperature needs to be realized by adapting to the temperature curve of the polymer adhesive film. In addition to reaching a certain temperature, this special polymer film also needs a considerable period of holding time. In order to achieve the best composite process, the equipment was finally positioned in the two-step method in the mid-1990s, that is, the prefabrication process. It is formed into a pe core board, which is then compounded with the upper and lower aluminum plates. This was also the international common practice at that time.
The main process is: extruder → three-roll calendering → conveying surface cooling → upper and lower aluminum plate uncoiling → upper and lower aluminum coils and polymer adhesive film bonding PE plate → compounding into plate → cooling and shaping →
Cross cutting, longitudinal cutting → finished product.
Zhejiang Geartech Machinery Co., Ltd. has long been committed to the research and development, manufacture and sales of hot-dip galvanized steel sheet production lines, color-coated steel sheet production lines, color-coated aluminum sheet production lines and aluminum-plastic composite sheet production lines. After years of practical experience and the requirements of customers around the world, it has developed into a professional equipment supplier in the industry.
Because of its professionalism, Geartech products are well received by the same industry and users.
Geartech is convinced that only professional people do professional things with professional hearts, can we maintain long-term and good common interests of you and me.
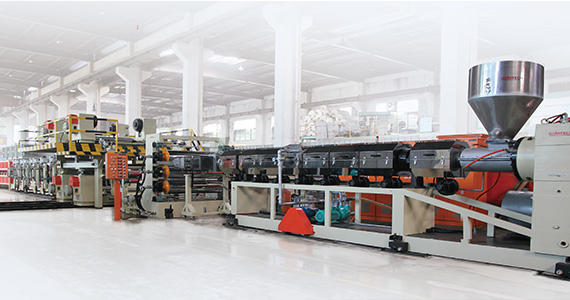